The process of creating a custom packaging box is a meticulous journey that involves creativity, precision, and a deep understanding of the client's needs. Custom packaging is a powerful tool for brands to stand out in a crowded marketplace, and custom packaging boxes are a key element in this strategy. Let's delve into the seven-step process of paper box printing and packaging, highlighting the importance of working with a custom packaging factory.
Step 1: Conceptualization
The journey begins with the conceptualization of the design. This is where the brand's vision and the packaging factory's expertise come together. The goal is to create a design that reflects the brand's identity and appeals to its target audience.
Step 2: Design Development
Once the concept is agreed upon, the design development phase begins. This involves creating detailed illustrations, selecting the right color palette, and finalizing the layout. Custom packaging factories often have in-house designers who can work closely with clients to bring their vision to life.
Step 3: Material Selection
The choice of material is crucial for the durability and aesthetic appeal of the custom packaging box. Paper is a popular choice due to its versatility and eco-friendliness. Custom packaging factories offer a range of paper stocks, from matte to glossy finishes, to suit different product types and branding requirements.
Step 4: Prototyping
Before full-scale production, a prototype is created. This allows the client to see and feel the packaging, ensuring that it meets their expectations in terms of size, design, and material. Any necessary adjustments can be made at this stage.
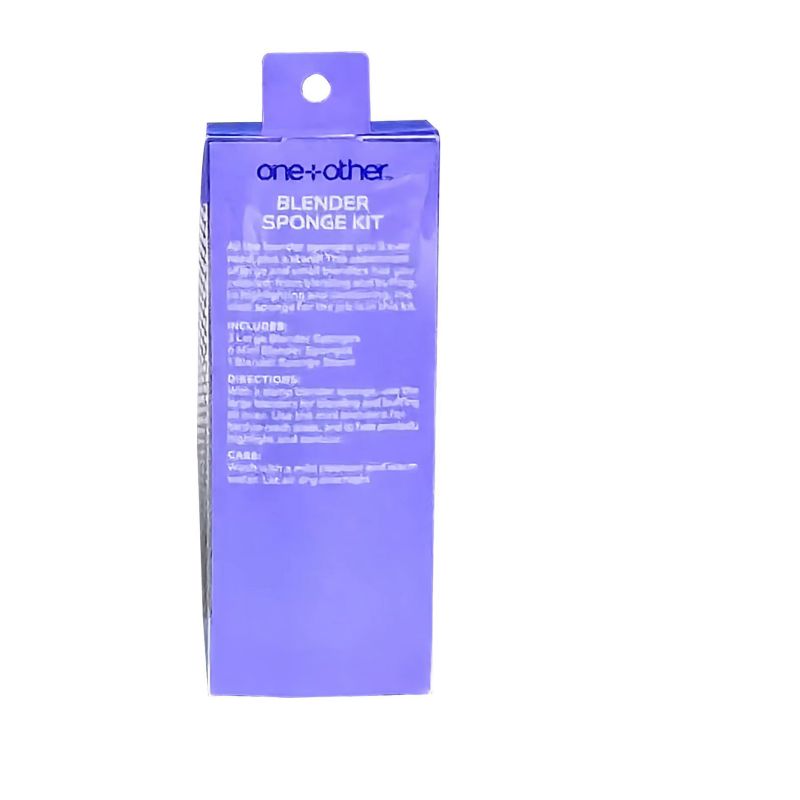
Step 5: Printing
The printing process is where the custom packaging box comes to life. Custom packaging factories use advanced printing techniques to ensure high-quality, vibrant images and text. The choice of printing method, such as offset or digital printing, depends on the complexity of the design and the quantity required.
Step 6: Finishing Touches
After printing, the packaging undergoes various finishing processes. This may include lamination for added protection, embossing or debossing for a tactile effect, and die-cutting to achieve the desired shape. Custom packaging factories have the equipment and expertise to apply these finishing touches with precision.
Step 7: Quality Control and Delivery
The final step is quality control, where each box is inspected for defects in printing, cutting, and overall construction. Once the boxes pass the quality check, they are packaged and delivered to the client.
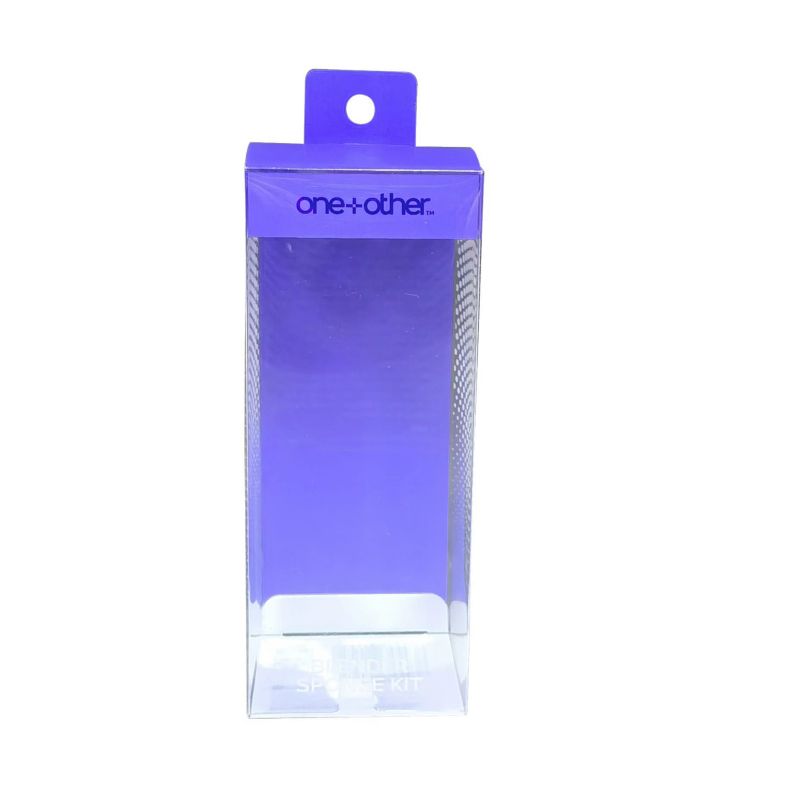
The Role of a Custom Packaging Factory
A custom packaging factory plays a pivotal role in the entire process. They not only provide the production capabilities but also contribute to the design and material selection. Their expertise ensures that the final product meets the highest quality standards and effectively represents the brand.
Benefits of Custom Packaging
- Brand Recognition: Custom packaging boxes help in building a strong brand identity.
- Market Differentiation: Unique packaging can set a product apart from competitors.
- Customer Experience: Attractive packaging enhances the unboxing experience, leading to customer satisfaction and loyalty.
The seven-step process of paper box printing and packaging is a testament to the craftsmanship and attention to detail required to create custom packaging boxes. By partnering with a custom packaging factory, brands can ensure that their packaging is not only functional but also a reflection of their brand's unique story. In a world where first impressions matter, custom packaging is more than a box—it's a silent salesperson.